Respiratory Protective Equipment (RPE) should only be used in the workplace after all other reasonably practicable measures to prevent or control exposure to harmful substances have been implemented.
COSHH and RPE Standards
Personal Protective Equipment (PPE) should be issued as a last line of defence
Regulations
The Health and Safety Work etc Act 1974 and the Management of Health and Safety at Work Regulations 1999 set out the basic requirements for employers to provide and maintain a safe working environment, so far as is reasonably practicable.
Control of Substances Hazardous to Health (COSHH) regulations sets out the legal requirements to protect workers from health risks caused from hazardous substances at work. COSHH states that, where it is not reasonably practicable to prevent exposure to a hazardous substance, control of that exposure should only be treated as adequate if:
- The principles of good practice for the control of exposure are applied
- Any workplace exposure limit (WEL) is not exceeded
- For a substance that has the potential to cause cancer or occupational asthma exposure is reduced to as low a level as is reasonably practicable
Employers Responsibility
Employers have a duty to carry out a suitable and sufficient risk assessment and take steps to ensure they prevent or adequately control exposure. Going through the risk assessment process, required by law, can determine whether the use of RPE is necessary in your workplace.
RPE may need to be used to satisfy requirements in the following pieces of legislations, additional to the COSHH Regulations 2022. These need to be considered as to whether the regulations apply to you and comply with any specific requirements they contain on RPE:
- Control of Asbestos Regulations 2012
- Control of Lead at Work Regulations 2002
- Ionising Radiations Regulations 1999
- Confined Spaces Regulations 1997
To be compliant, RPE used in the workplace must be CE-marked. This ensures the piece of equipment has been manufactured in accordance with the Personal Protective Equipment Regulations 2002 and meets the minimum legal requirements for its design. Whilst the four-digital code is used to identify the body responsible for checking manufacturing quality, it does not indicate that the piece of equipment is adequate or suitable for use in the workplace. It is the employers' responsibility to select the correct RPE to meet the specific requirements.
Is PPE the Right Control?
RPE can be uncomfortable to wear and interfere with work, which can lead to incorrect use. It is important for any RPE provided to be worn properly and maintained to ensure the wearer receives the required protection.
You should only select and use RPE:
- Where an inhalation exposure risk remains after you have put in place other reasonable control
- While you are putting in place other control measures
- For emergency work or temporary failure of controls where other means of control are not reasonably practicable
- For short-term or infrequent exposure, such as maintenance work, where you decide that other controls at the source of the exposure are not reasonably practicable
Respiratory Protective Equipment EN Standards
For effective protection which complies with the legal standards, you must ensure that your chosen equipment has been tested to the relevant EN standards for RPE:
More from Arco
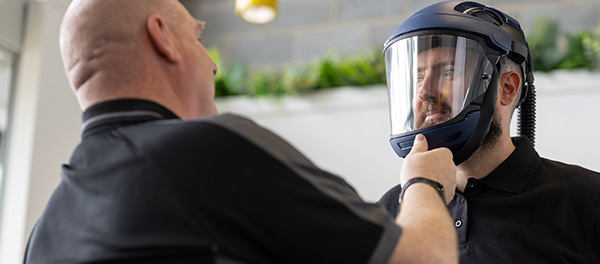
Product Selection
Selecting both adequate and suitable RPE is vital to ensure the correct level of protection is issued. One size facepiece does not fit all which is why it’s important to supply RPE that is specific for the risk and best fits the wearer.

Our Range
Our extensive range of respiratory protection equipment offers protection against a variety of hazards, is designed to suit a variety of work situations and available in a variety of styles to match the requirements of the wearer.